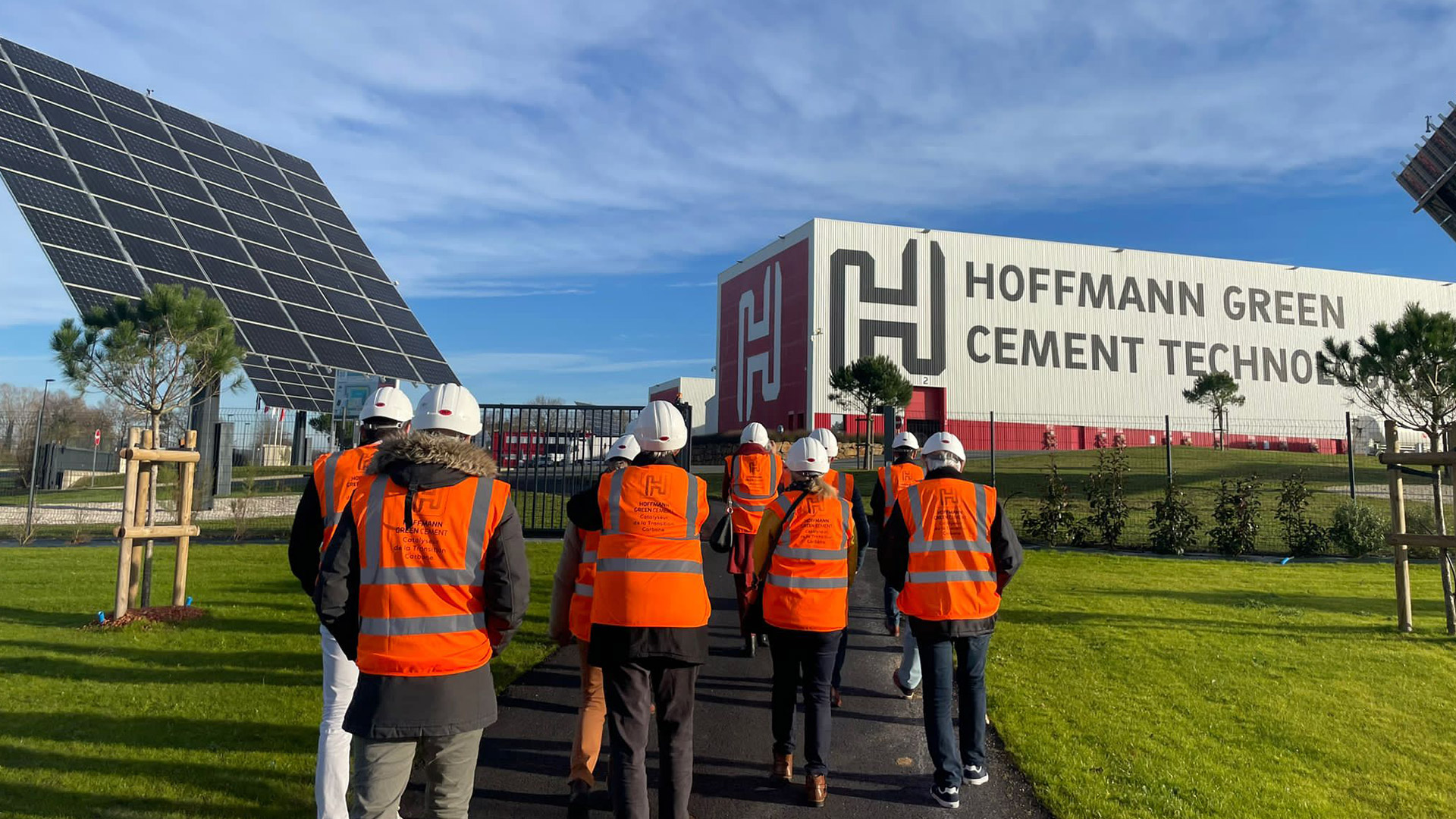
Themanufacture of traditional cement is highly polluting. In particular, it requires a lot of energy to produce clinker, the main component of cement. To reduce its carbon footprint by 80% by 2050, the cement industry must therefore innovate.
Hoffmann Green is fully committed to this mission. The ciment decarbonated 0% clinker and with low energy consumption is already an accessible reality. We have developed 3 types of clinker-free cement (H-P2A, H-UKR, H-EVA), which significantly reduce CO2 emissions. Today’s key challenge is to reduce the environmental impact of future construction.
To understand the carbon impact of traditional concrete
From its extraction to its shipment to the various construction and public works sites where it is used, the process of manufacturing and transporting traditional cement (the main component of concrete material) is proving very heavy in terms of carbon impact. The example of Portland cement (or CEM1) is significant in this respect: it is the cement most commonly used in the manufacture ofreinforced concrete or prestressed concrete. Initially, Portland cement is extracted from production quarries as a raw material, then crushed, dried and ground. This initial phase still has little impact in terms of carbon footprint.
Then things get complicated, as the material is fired (or clinkerised) at a very high temperature (1,450°C) over a very long period (18 hours), before the clinker obtained is stored. This extremely energy-intensive phase is responsible for the poor carbon footprint of traditional concrete, a material that does not pollute as such, but rather because of the way it is manufactured. The final stages of production (mixing and admixture, grinding, packaging and shipping) have only a marginal impact on the carbon footprint of Portland cement.
0% clinker low-carbon concrete: what is it?
Since the carbon impact of traditional concrete is largely due to the clinkering of the cement, it is therefore this particular aspect that needs to be addressed to achieve a significant gain in terms of carbon footprint. And this is precisely what we are proposing with our zero clinker 0% decarbonised cement and low energy consumption, in every way revolutionary compared to the standard process previously outlined.
First and foremost, it is a manufacturing process based on a mixture of co-products (slag, clay, gypsum) that are not quarried (with all the environmental drawbacks associated with mining), but supplied by local producers, in a move to promote the local and circular economy. The exclusivity of the Hoffmann Green method then lies in the cold activation, i.e. the fabrication without firing of our cements (i.e. 0% clinker). The final production phase (mixing and admixture, packaging and shipping) is also more virtuous, as it does not require grinding as with CEM1. So it’s no exaggeration to talk about a revolutionary production method, with a cement that cuts its carbon footprint by a factor of 5.
Hoffmann Green 0% clinker low-carbon cement technologies
Hoffmann Green is proud to offer 3 new low-carbon cement technologies to the entire building industry. Technologies that foreshadow the new generation of buildings, in line with the ecological and environmental imperatives to which we must all collectively respond. 3 decarbonated cements for all technical applications in sustainable construction: staircases, kerbs, slabs, prefabricated walls, blockwork, gutters, drainage paving, foundations and concrete blocks are among the applications on offer.
With these 3 innovations, low-carbon concrete is already a reality, available in 3 types of cement without clinker and using co-products available in abundance, not requiring recourse to the usual mining resources.
Our 3 clinker-free cement innovations
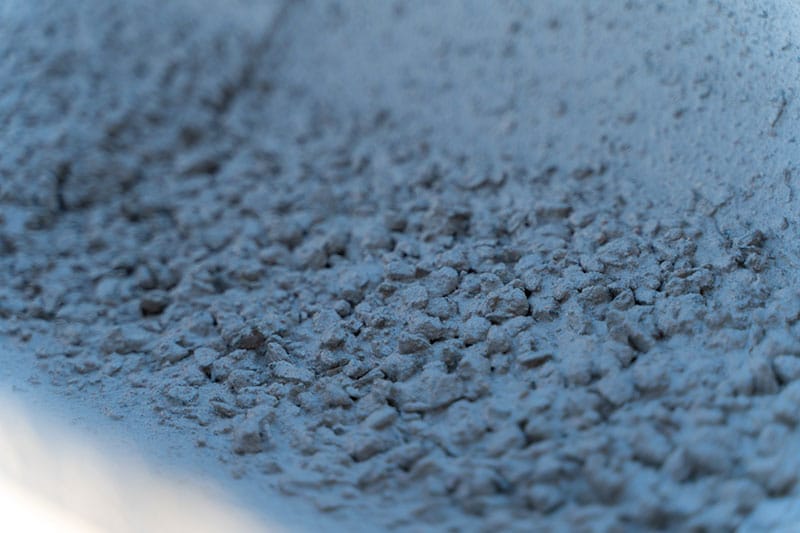
- H-P2A : a low-carbon cement made from flash clay and silicate, plus activators and superactivators (the flash clay being a co-product from local clay sludge). A resistant cement that comes in the form of a geopolymer solution to produce a 100% mineral, non-flammable, VOC-free adhesive.
- H-EVA: a low-carbon cement made from flash clay and gypsum / desulphogypsum, to which activators and superactivators have been added. An innovative binder, H-EVA is an alkaline ettringitic technology, ideal for road manufacture as well as mortars and site concretes.
- H-UKR: a low-carbon cement made from blast-furnace slag with added activators and superactivators. Blast furnace slag is a co-product of the metallurgical industry (thus promoting the circular economy). H-UKR is particularly effective in the construction sector, especially for ready-mixed concrete and in-plant precast concrete.
These innovative processes do not involve baking, but cold chemical reactions between materials using activators. The materials used are co-products from other industries: metakaolin clay, gypsum, blast furnace slag and sodium metasilicate. The objective (achieved) being to deliver a low-carbon 0% clinker cement with low energy consumption for greener concrete that respects the environment and future generations.
High-performance 0% clinker low-carbon cements
Our cements have acarbon footprint up to a factor of 5. This ecological performance goes hand in hand with technical performance that is equivalent to, if not better than, that of conventional cements :
0% clinker, low-energy and environmentally friendly cements
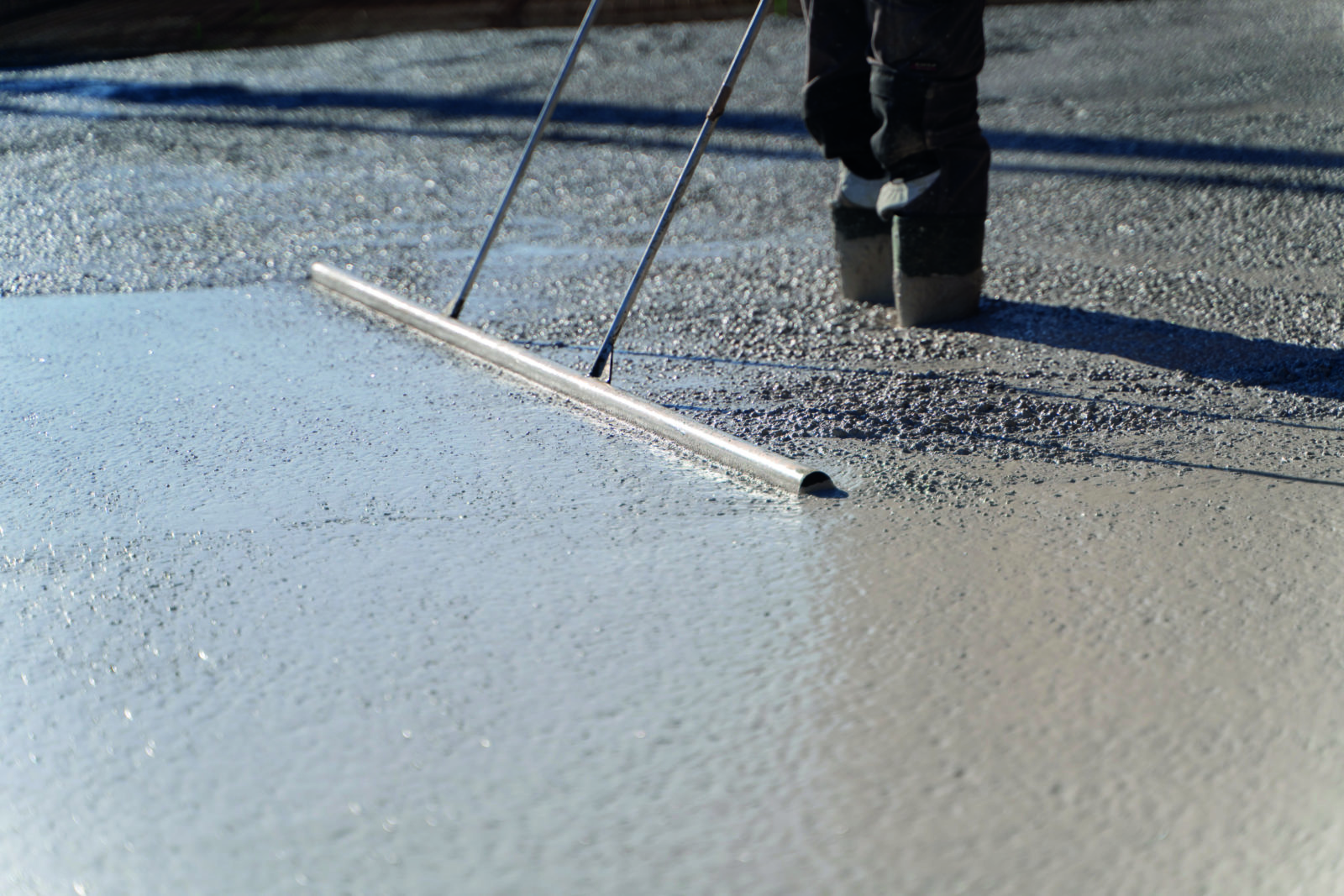
The main source of CO2 and greenhouse gas (GHG) emissions in the manufacture of concrete is the manufacture of cement.
Our cements make it possible to obtain a low-carbon concrete, thanks to the absence of clinker, 95% of which is used in conventional Portland cement (CEM I) and comes from a highly emissive process (quarrying, transport, firing using fossil fuels, grinding).
Hoffmann Green cement is ideal for use in engineering concretes (self-placing, special foundations, screeds) and prefabrication.