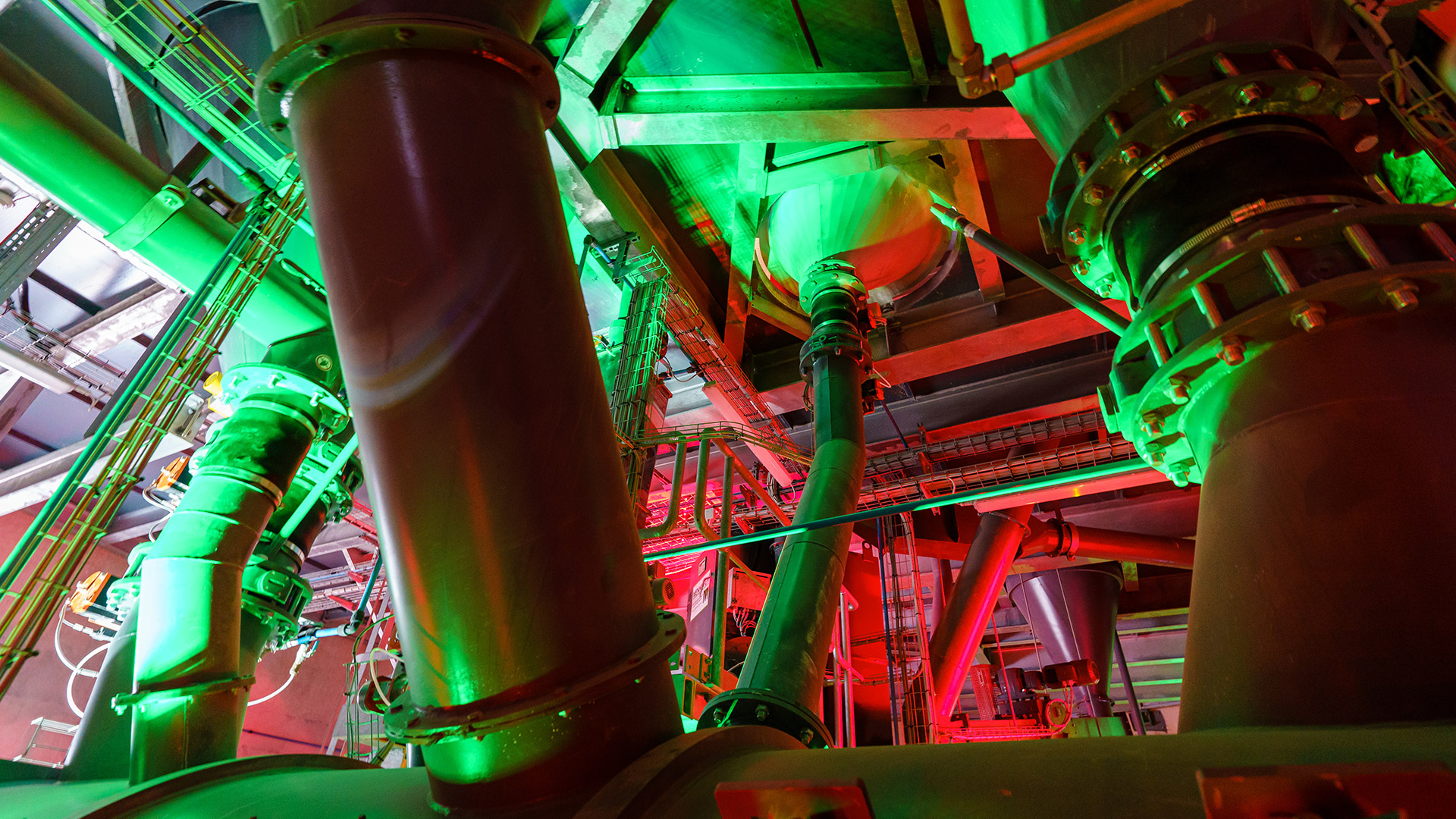
Portland cements
Producing conventional cement requires the extraction of quarried rock. Once extracted, these rocks are crushed, transported and then stored in pre-homogenization halls.
The mixture of crushed rocks is dried and crushed to obtain the “raw”. This is then pre-calcined at 850°C before being fired in a rotary kiln around 1,450°C. This process is energy intensive due to the high temperature to be maintained in the oven 24/7.
Firing is the site of chemical chain reactions, aimed primarily at transforming molecules into oxides to formclinker. Thus, limestone (CaCO₃) breaks down into CaO and CO₂, thus inducing a significant emission of CO₂. This clinker is then cooled, then ground with additions to produce cement..
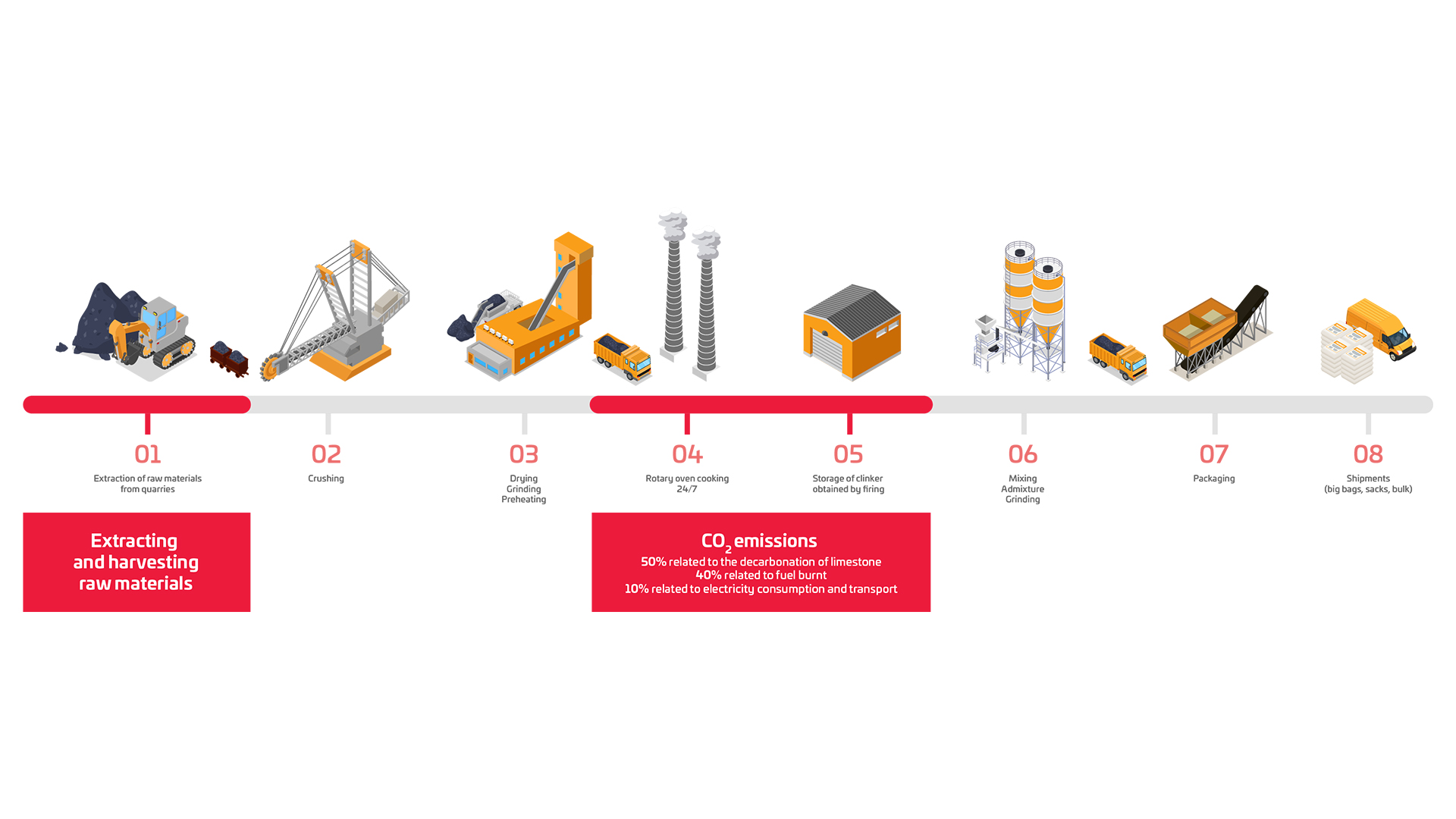
A model redesigned by Hoffmann Green
No clinker, no firing, cold-activated to divide CO₂ emissions by 5.
Hoffmann Green cements activated in a cold process are made from co-products from industry, such as blast-furnace slag, clay sludge and gypsum. Activators and superactivators are added in very precise doses during the manufacturing process, enabling Hoffmann Green 0% clinker decarbonated cements to be produced without firing and with no impact on natural resources.
Our 4.0 production units are in line with our principle of minimizing environmental impact. Through the logic of the circular economy and recycling, they produce no waste and use renewable energies to power our sites.
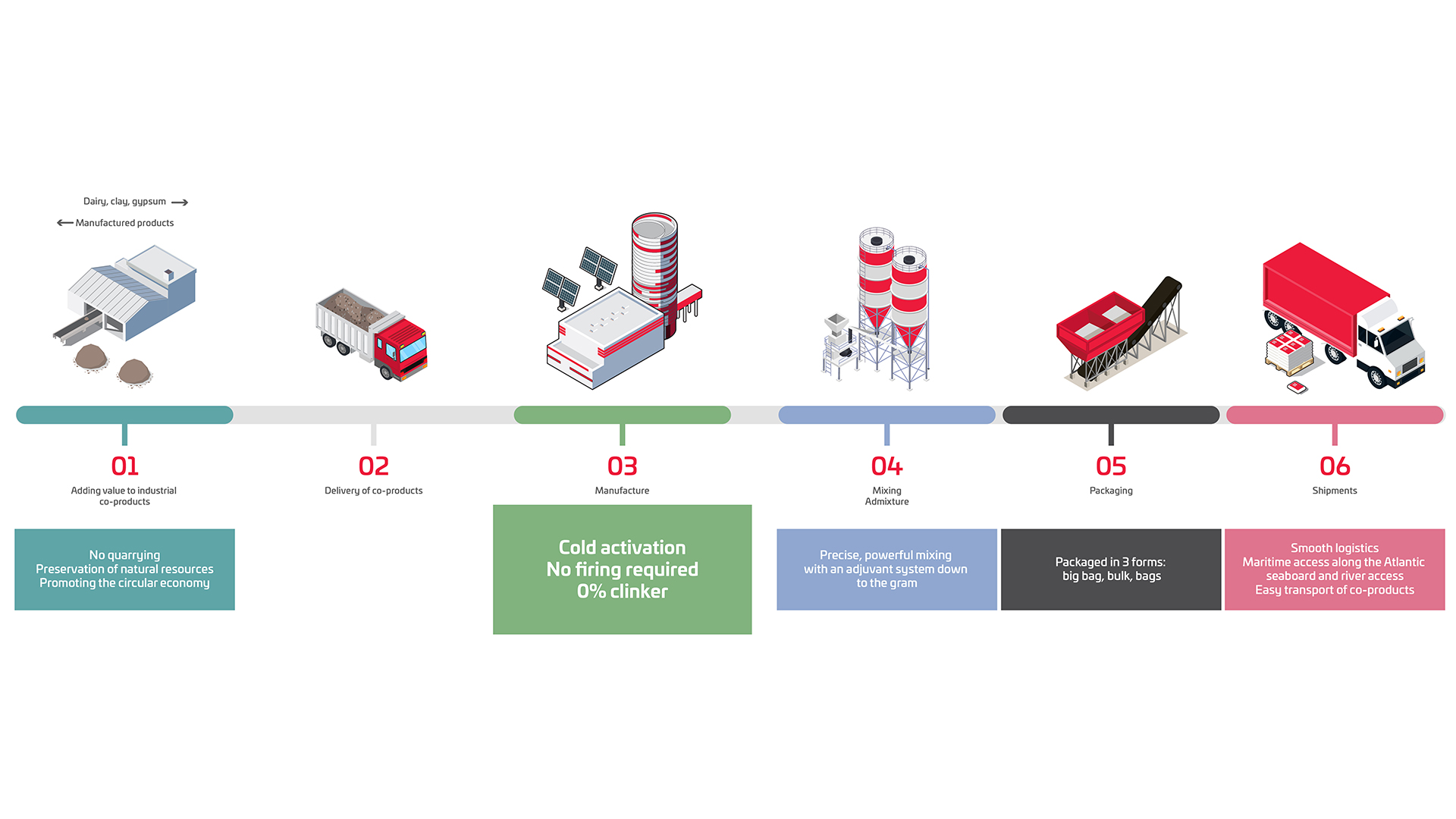
A manufacturing process based on the principles of the circular economy
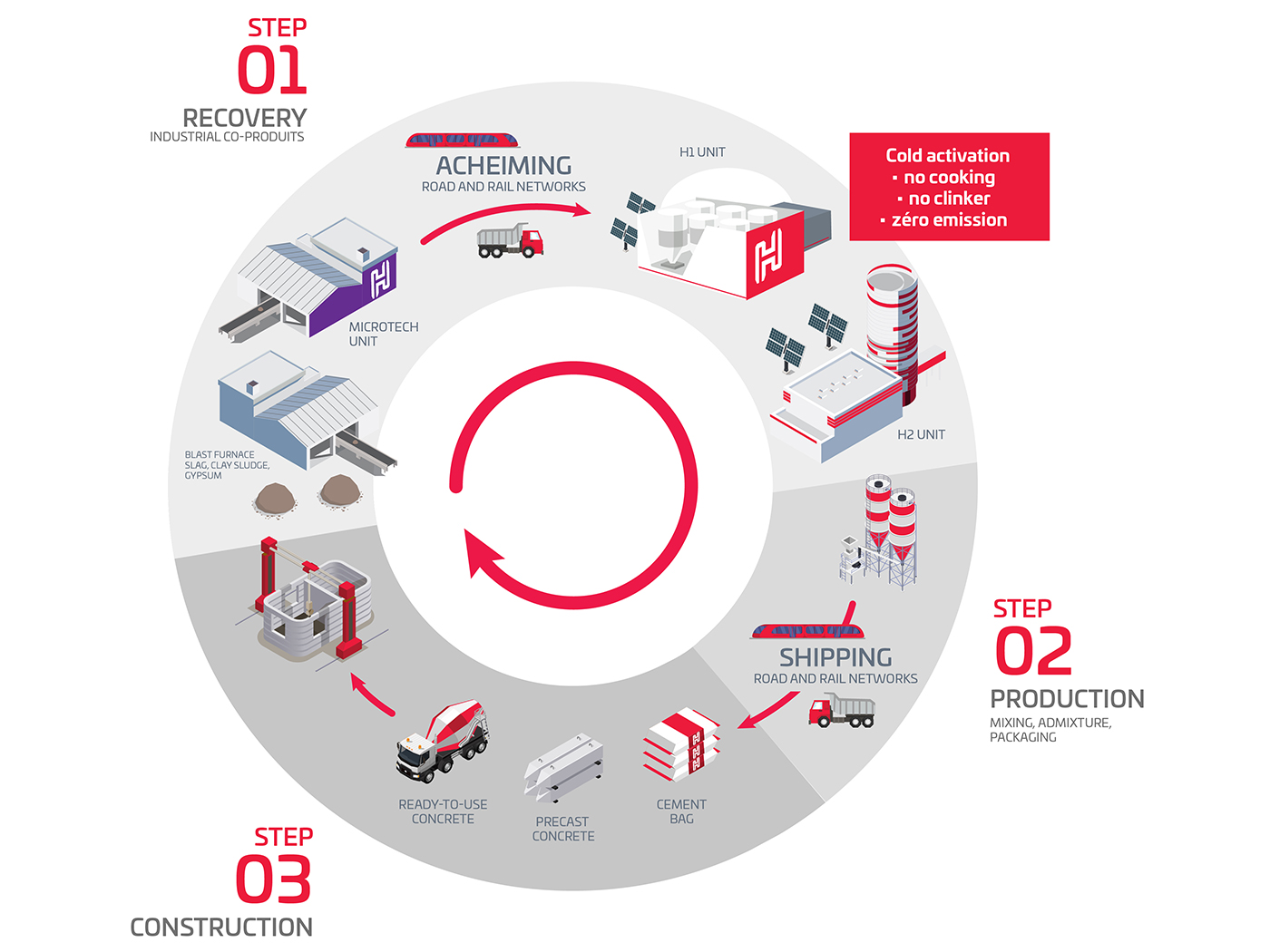
Hoffmann Green recovers and valorizes by-products from industry and construction, transported to our production plant:
- Blast furnace slag comes from the metallurgical and iron and steel industries.
- Flashed clay is a co-product of clay sludge.
- Gypsum/desulfogypsum is a by-product of construction site overburden.
These coproducts, present in abundance, are mixed with our activators and superactivators specifically formulated by Hoffmann Green and thus give birth to our revolutionary cements.
A clean, revolutionary cold manufacturing process
Hoffmann Green is at the origin of a technological breakthrough based on the modification of cement composition so that it does not contain clinker, the main source of CO₂ emissions in traditional cement production, as well as on the creation of a clean, cold cement manufacturing process (no firing of raw materials).
The manufacturing process for Hoffmann Green cements is based on the systematic use of abundant co-products as a substitute for natural resources. This innovation makes it possible to produce a decarbonated 0% clinker cement with low energy consumption, while preserving natural resources, in particular without resorting to quarrying. Thus, thanks to the absence of a firing process, the carbon impact of Hoffmann Green cements is significantly reduced compared to the traditional cement manufacturing process.
Admixture and mixing are at the heart of our industrial process. This is followed by the packaging of our cements (big bag, bulk or sacks), then shipment to the worksite areas according to an optimized transport scheme (see animation above).
In a context of climate emergency and energy price inflation, Hoffmann Green is actively participating in the energy transition by producing a clean cement that consumes 10 to 15 times less energy than Portland cement, thanks to its 4.0 production site powered by a fleet of solar trackers and soon two additional sites.
Cement that supplies three main markets
Far from the image of traditional cement plants, Hoffmann Green’s industrial layout allows its plants without kilns or chimneys to be located as close as possible to urban areas of major construction.
Hoffmann Green cements thus cater for the three main cement markets:
- Prefabricated concrete: prefabrication of concrete products outside their final location and assembly/delivery on site.
- Ready-to-use concrete (RTC): concrete prepared in factories in concrete batching plants, then transported to the place of use in mixer trucks.
- Cement bags: marketed to professionals and the general public, our bags will soon be distributed through 5,500 distribution points in France.