- 01Reducing cement’s carbon footprint
Cement production alone accounts for 7% of CO₂ emissions worldwide. The new 0% clinker and low-energy cements developed by Hoffmann Green cut CO₂ emissions by almost 5 compared with traditional Portland cement (CEM I), thanks to a new industrial process of cold activation, without a kiln.
- 02Start-up of “H2”, the world’s first vertical cement plant
This new plant, with a production capacity of 250,000 tonnes, compared with 50,000 tonnes for the industrial pilot plant, has been operational since summer 2023. Its vertical design reduces the land footprint and associated soil sealing, and preserves natural spaces. This vertical plant is designed for a gravity-fed production mode, using the materials’ own weight in the industrial process, enabling significant energy optimization.
- 03Ongoing, voluntary approval process for Hoffmann Green’s innovative cements
Approval involves the certification of solutions that have already been standardized: H-IONA and slag ground at the Hoffmann Microtech plant. Certification involves continuous monitoring of performance consistency.
The second pillar of certification involves the evaluation of breakthrough solutions.
Bringing new cements to market involves a long and costly standardization process. Hoffmann Green is CSTB’s second largest customer after the French government. This close partnership now enables us to market low-carbon breakthrough innovations that offer the same guarantees and, at the very least, the same performance as traditional cements. This voluntary approach is carried out in full transparency to support the market in deploying these solutions.
- 04A commitment to reforestation to store carbon
For its contribution to carbon sinks, Hoffmann Green signed a partnership with Reforest’Action in 2018. Within this framework, Hoffmann Green supported the planting of 10,000 trees during the 2019-2020 season in Occitanie. Certified B Corp, Reforest’Action is a company with a social vocation created in 2010 by Stéphane Hallaire, whose first mission is to make as many people as possible aware of the power of forests and the need to protect them, and the second to take action by preserving and restoring forests in France and around the world.
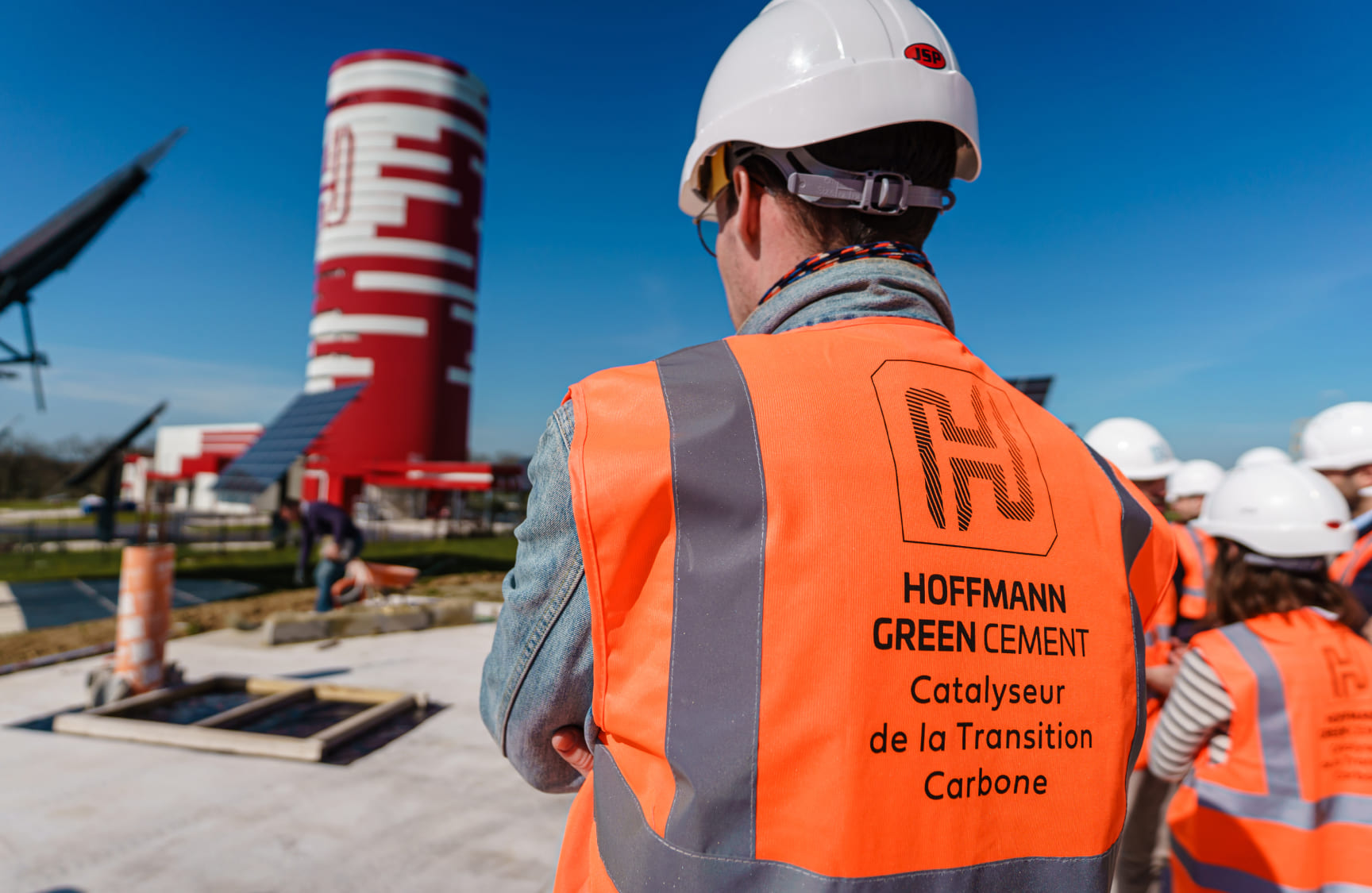
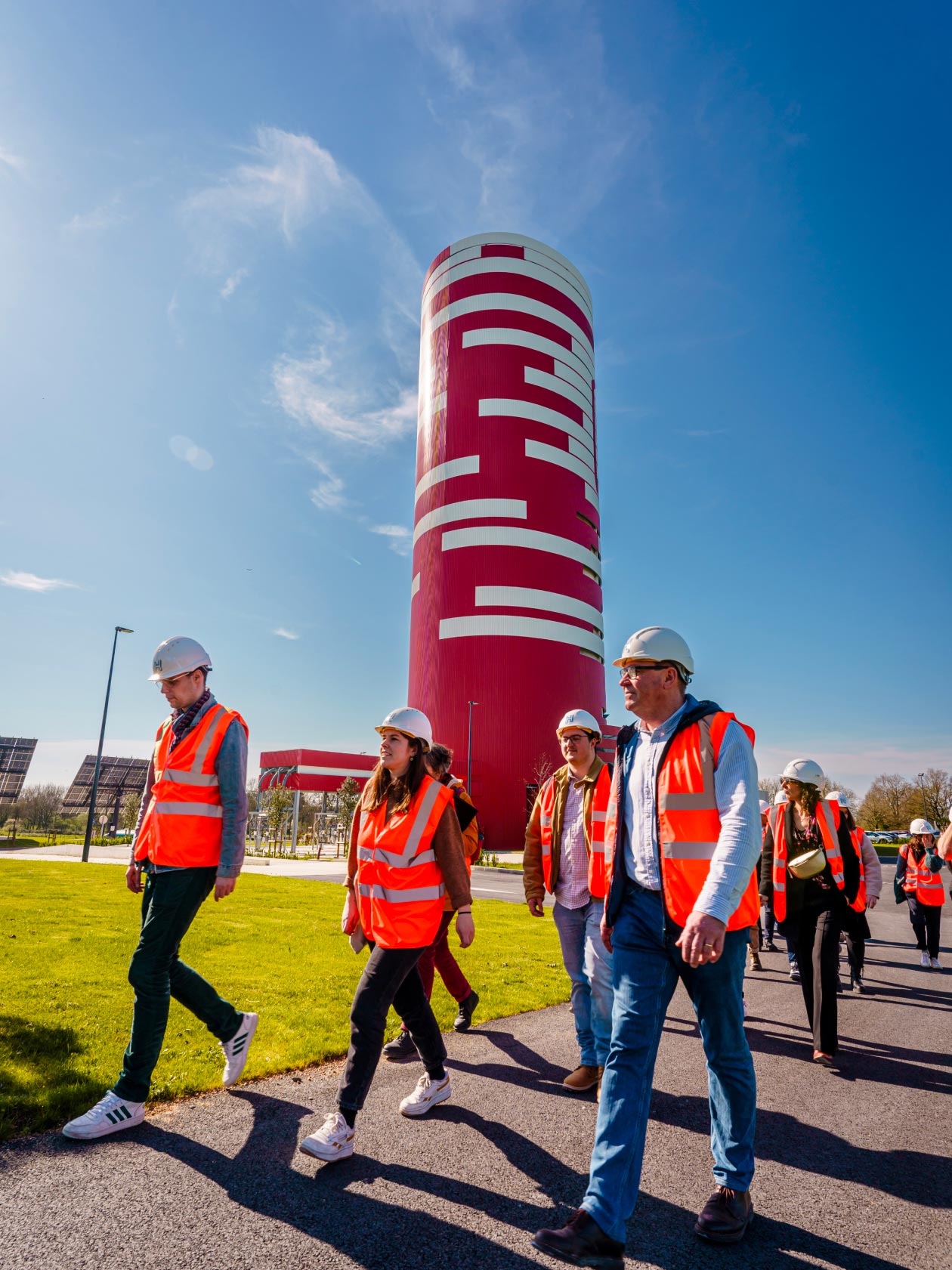
CSR as the backbone of development
Since its creation in 2016, Hoffmann Green has been focusing its efforts on developing new decarbonised 0% clinker cements and thus contributing to decarbonisation. The company, by the very nature of its business, addresses the challenges associated with CO₂ emissions. Thus, the more Hoffmann Green produces, the more CO₂ emissions will be avoided, and the more resources will be preserved.
Still a young company, Hoffmann Green has been committed, since its creation, to a progressive approach to building a global CSR strategy. In 2020, external assessments provided an overview of the issues facing Hoffmann Green.
- 8,486 tonnes8,486 tonnes of CO₂ avoided in 2023. The tonnes of CO2 avoided are calculated by the gain in CO₂ achieved through the replacement of a traditional cement, based on the current cement consumption mix, with Hoffmann Green Cement clinker-free decarbonated cement.
- 17,289 tonnes17,289 tonnes of extracted limestone avoided in 2023. In 2023, the use of Hoffmann Green cement without clinker avoided the extraction of 17,289 tonnes of limestone that would have been required for equivalent production with traditional cement.
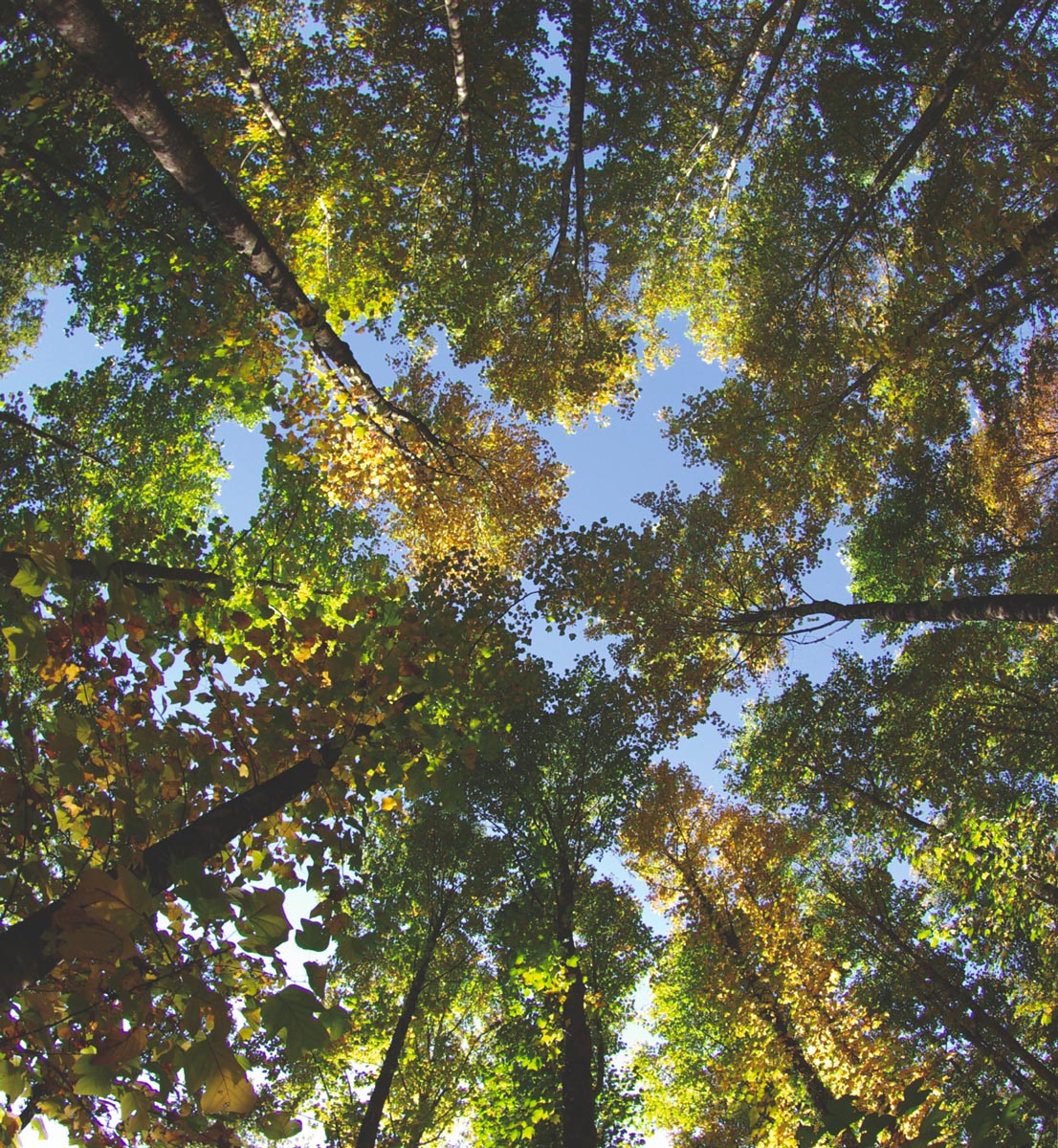
Hoffmann Green’s CSR policy
Hoffmann Green’s new clinker-free low-carbon cements aim to reduce the construction sector’s carbon footprint.
But the company’s business also involves it in other ways. Since its creation, Hoffmann Green has been committed to developing a comprehensive and progressive CSR approach to support the company’s development. Today, this policy is organised around three key areas:
- Responsible producer /
It means minimising the environmental footprint and preserving resources. - Responsible employer /
It means ensuring optimum conditions for the development of new jobs and new professions linked to the company’s activity. It also means working on employee health and safety issues. - Responsible partner /
It means putting quality at the centre of our approaches. It also means thinking about modes of governance to meet the expectations of all stakeholders.
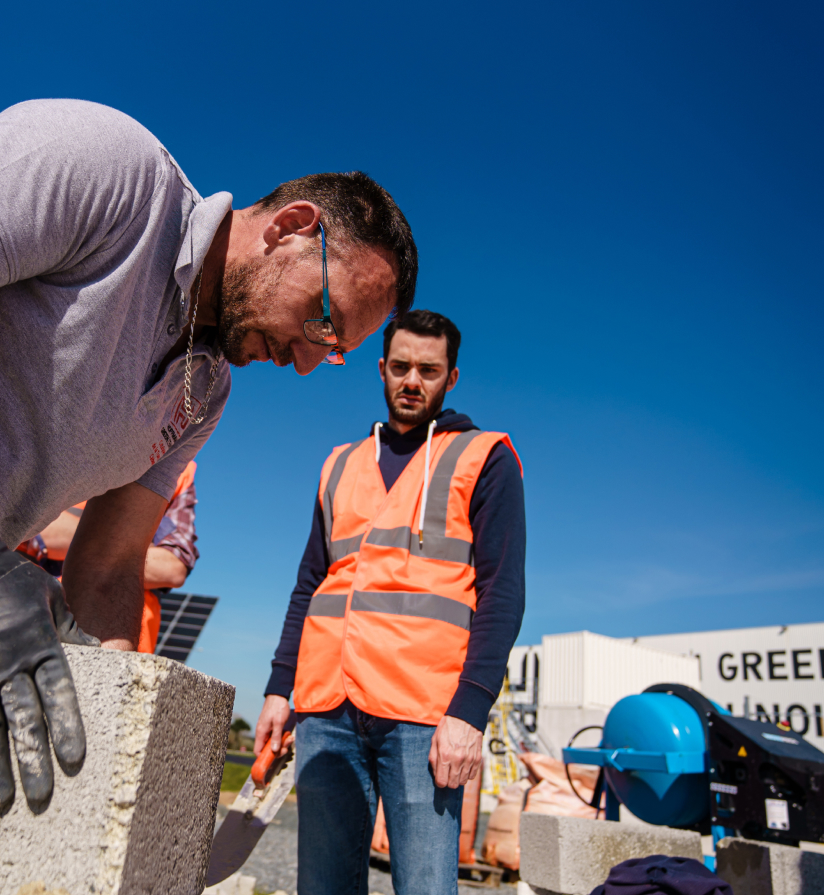
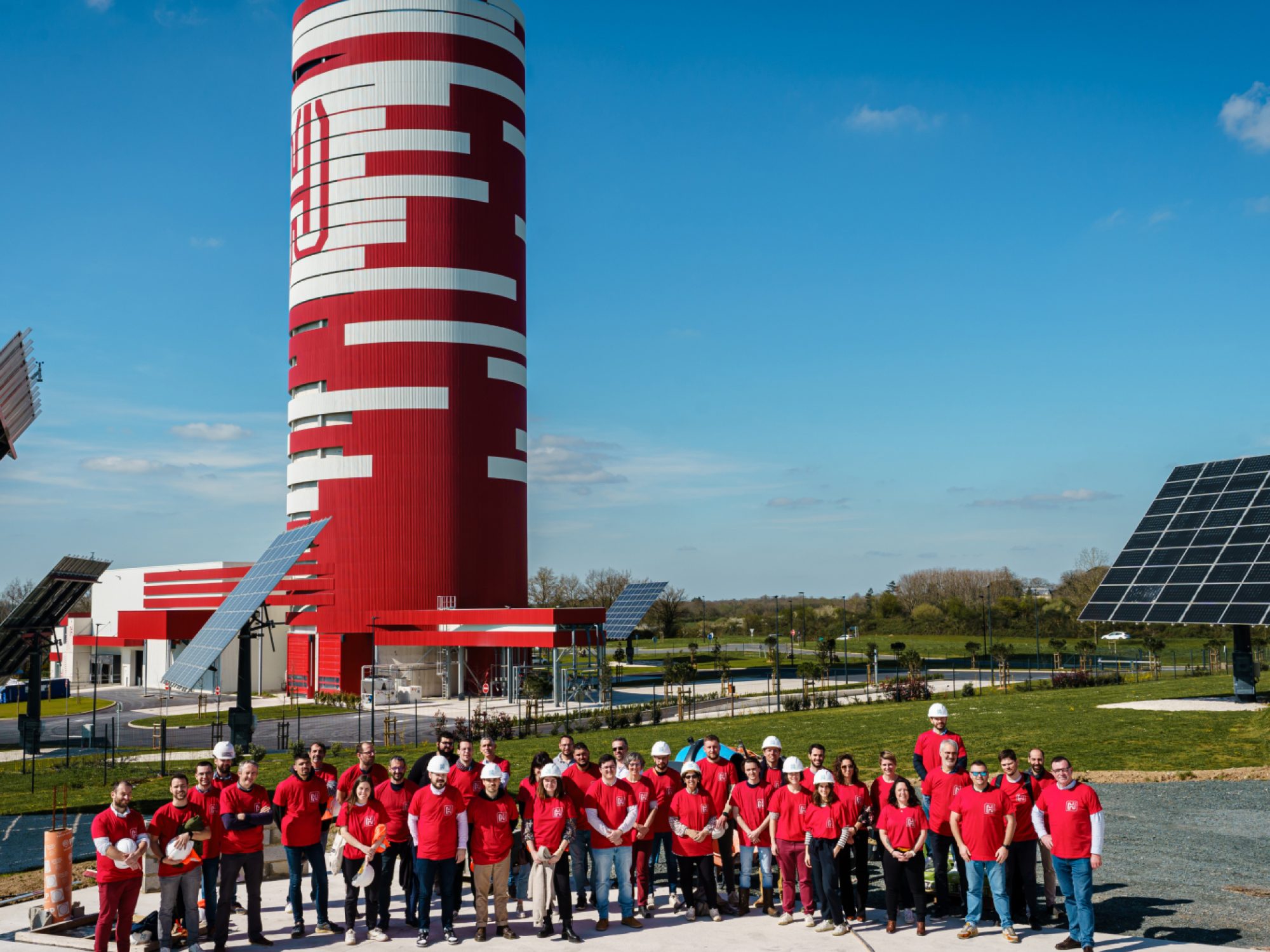
Reducing our carbon footprint
Preserving natural resources
- 01Favoring green electricity
Hoffmann Green uses solar trackers to generate and consume almost a quarter of its energy needs directly on its production site. By the end of 2022, the number of solar trackers had risen from 3 to 12.
To complement this self-consumption, in 2020 Hoffmann Green signed a green electricity purchase contract with Engie to cover 100% of its consumption.
- 02Reduce the use of natural resources
In 50 years, resource extraction has more than tripled worldwide. In 2017, the world extracted nearly 44 billion tonnes of non-metallic minerals (sand, gravel, clay).
Quarried limestone is the raw material for traditional cements. A source of nuisance for the environment and local residents, quarries also damage biodiversity. There are 3,600 active quarries in France, including around 500 that extract around 418,300 m³ of limestone per year.
The preservation of resources is at the heart of Hoffmann Green’s action. All solutions developed by Hoffmann Green use co-products (blast furnace slag, clay sludge, gypsum and desulfogypsum) as raw materials. In use, Hoffmann Green cements require no more sand and water than traditional cements. - 03Reduce the amount of industrial waste
Based entirely on the principles of the circular economy, Hoffmann cements’ production process valorizes industrial by-products, which become the main raw material for decarbonated cements. This virtuous approach is applied at every stage of the production process, which itself generates no waste. Incoming products are delivered by lorry, stored in tankers and transferred to the production line by automated conveyors. No packaging is used.
Developing new, high-quality industrial jobs
- 01Systematic annual performance reviews with each employee
Individual interviews enable us to take stock of each employee’s position, potential career development and training needs. Given the company’s young age and size (52 employees in 2023), each position is new and unique. As a result, each employee has a defined area of competence and responsibility.
- 02Distribution of free shares to all employees
Following the IPO, Hoffmann Green’s Board of Directors decided to involve all employees in the company’s future development. All Hoffmann Green employees are shareholders in the company. Thus, 0.3% of the capital is held by employees.
- 03Focus on long-term employment
Hoffmann Green favors long-term employment, with a predominance of permanent contracts (98.8% in 2023), enabling the company to build long-term relationships with its employees. All employees are on long-term contracts, with the remainder on apprenticeship contracts that enable the gradual integration and training of young professionals.
Taking action for health and safety at work
- 01Setting up an occupational health and safety management system
The start-up of the first pilot plant was accompanied by the introduction of a safety policy under the responsibility of the operations manager. Production teams were asked to draw on their experience to establish safety criteria adapted to the production process.
- 02Dust management at the plant
Specific measures have been taken to limit dust in order to guarantee air quality for operators in the plant. All production is carried out in a closed process to limit air contact with the products. In December 2019, an assessment of dust exposure was carried out by Carsat. This provided an overview of the situation and the actions to be taken in this area in the first pilot plant. This initial feedback has been incorporated into the plans for the H2 plant.
- 03Setting up Quality of Working Life (QWL) interviews
With the gradual increase in the number of employees, Hoffmann Green pays particular attention to collective dynamics and the well-being of each individual. Three group seminars are organised each year to share strategy and the role of each member of staff. At the same time, an annual interview on quality of life at work is organised, in addition to the individual interview. The aim is to discuss issues such as workload, work-life balance and job satisfaction.
Guaranteeing quality
- 01World’s first clinker-free cement validated under ATEx case A by CSTB
After four years of physical, chemical and mechanical testing, H-UKR cement has been awarded a technical assessment (ATEx case A) by the CSTB, the public body that guarantees the quality and safety of buildings. This assessment covers a very wide range of structures, from single-family homes to high-rise buildings for structural applications (floors, walls, beams, columns, etc.). H-UKR cement-based concrete structures are designed in accordance with Eurocode 2 and Eurocode 8, calculation standards recognised in France and Europe. The Technical Evaluation of Products and Materials (TPM) for H-UKR technology has just been enhanced. It provides a more objective assessment of the durability and quality of H-UKR cement, validating its expected service life of 100 years, thus paving the way for the use of H-UKR cement-based concrete in engineering structures (bridges, tunnels, etc.).
- 02Two new favourable assessments by the CSTB for H-UKR
Since 2022, Hoffmann Green has been pursuing the assessment plan for its H-UKR cement, obtaining two new assessments issued by the public authority that sets the benchmark for quality, durability and safety in buildings.
These ATEx assessments validate the use of H-UKR cement-based concrete for superstructure and foundation applications in all types of buildings: homes, public buildings, service sector buildings, high-rise buildings, etc.
It covers all applications for the internal and external structure of buildings: footings, stringers, rafts, floors, columns, beams, walls and slabs.
Since 2025, the infrastructure applications of H-UKR cement have been validated by an Avis Technique (ATec).
- 03Customer-focused continuous quality control
To guarantee the quality of these new cements, Hoffmann Green has set up a quality control system at every stage of production. To coordinate this monitoring and guarantee the same level of standards, a number of people have been specifically recruited.
- 04Development of the Quality laboratory
Hoffmann Green has developed a Quality laboratory with a dedicated team working directly with the production teams. A laboratory has been set up on the production site to optimise quality monitoring. The new equipment deployed and the quality monitoring methodology have enabled H-IONA cements to obtain AFNOR certification.
In 2023, a quality laboratory was also deployed at the Hoffmann Microtech plant.
- 05Validation of technical assessments of products and materials (ETPM)
Carried out by the Centre Scientifique et Technique du Bâtiment (CSTB), technical assessments of products and materials (ETPM) guarantee the durability and mechanical performance of our cements. These ETPMs enable Hoffmann Green to obtain experimental technical assessments (ATEx). Created on the initiative of the CSTB and the construction industry, the ATEx is a rapid technical assessment procedure formulated by a group of experts for any innovative product, process or equipment.