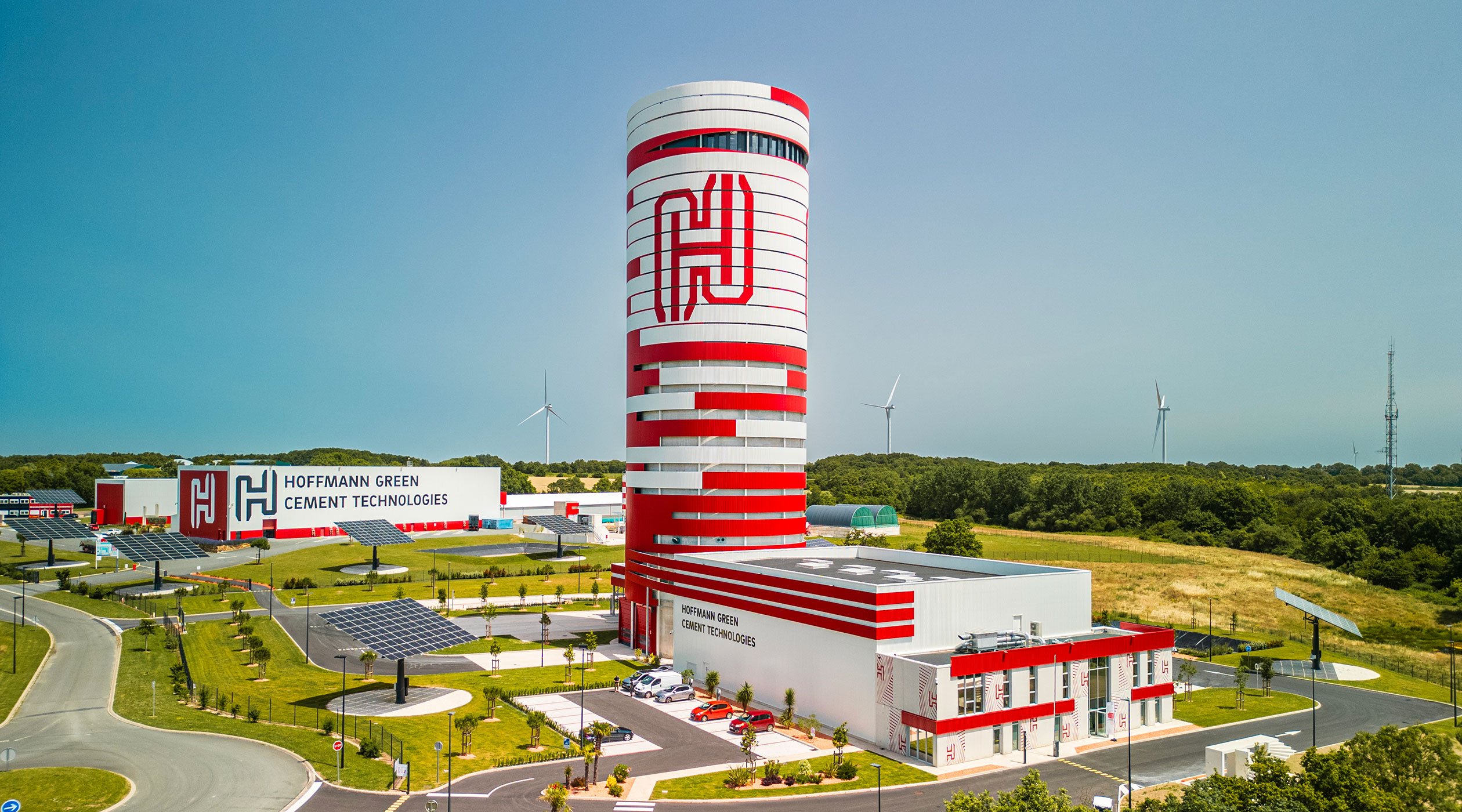
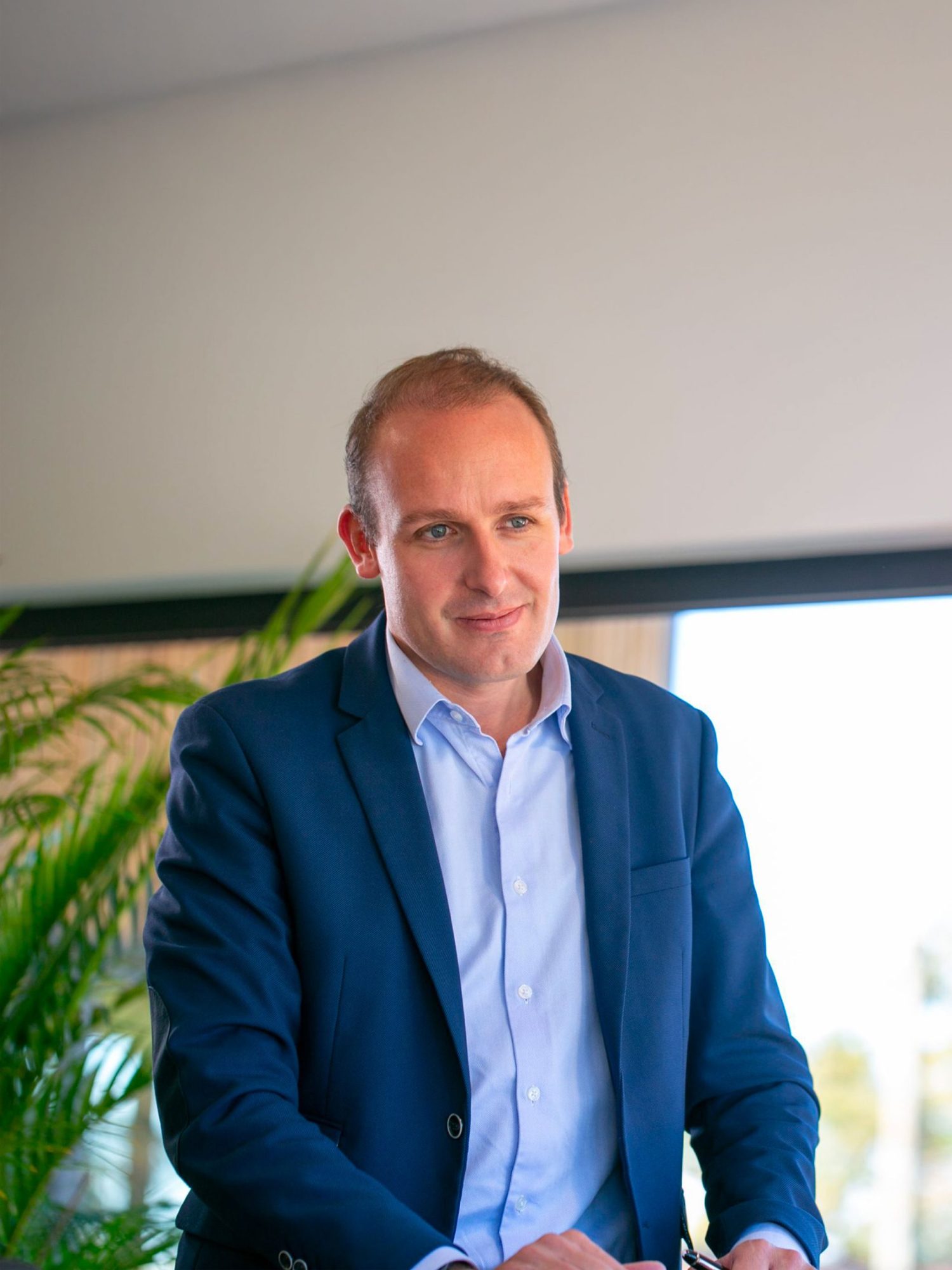
A vertical factory unique in the world
This new production unit, still at our historic site in Bournezeau (85), marks an important step in the company’s development.
This plant, the only one of its kind in the world, is a concrete example of our industrial vision: cutting-edge technologies, advanced R&D and human collaboration to offer solutions to environmental challenges.
We believe in the virtues of industry in tackling today’s challenges.
This new factory model will enable us to move away from an industry that has been subjected to the pressures of the past, with a high impact on its environment, to a desired industry that is at the cutting edge of technology and at the service of environmental issues.
<By increasing our production capacity by a factor of 8, from 50,000 to 400,000 tonnes, H2 is helping to accelerate our development and enabling us to meet the growing demand for our low-carbon cement without clinker.
Chairman of the Management Board of Hoffmann Green Cement Technologies
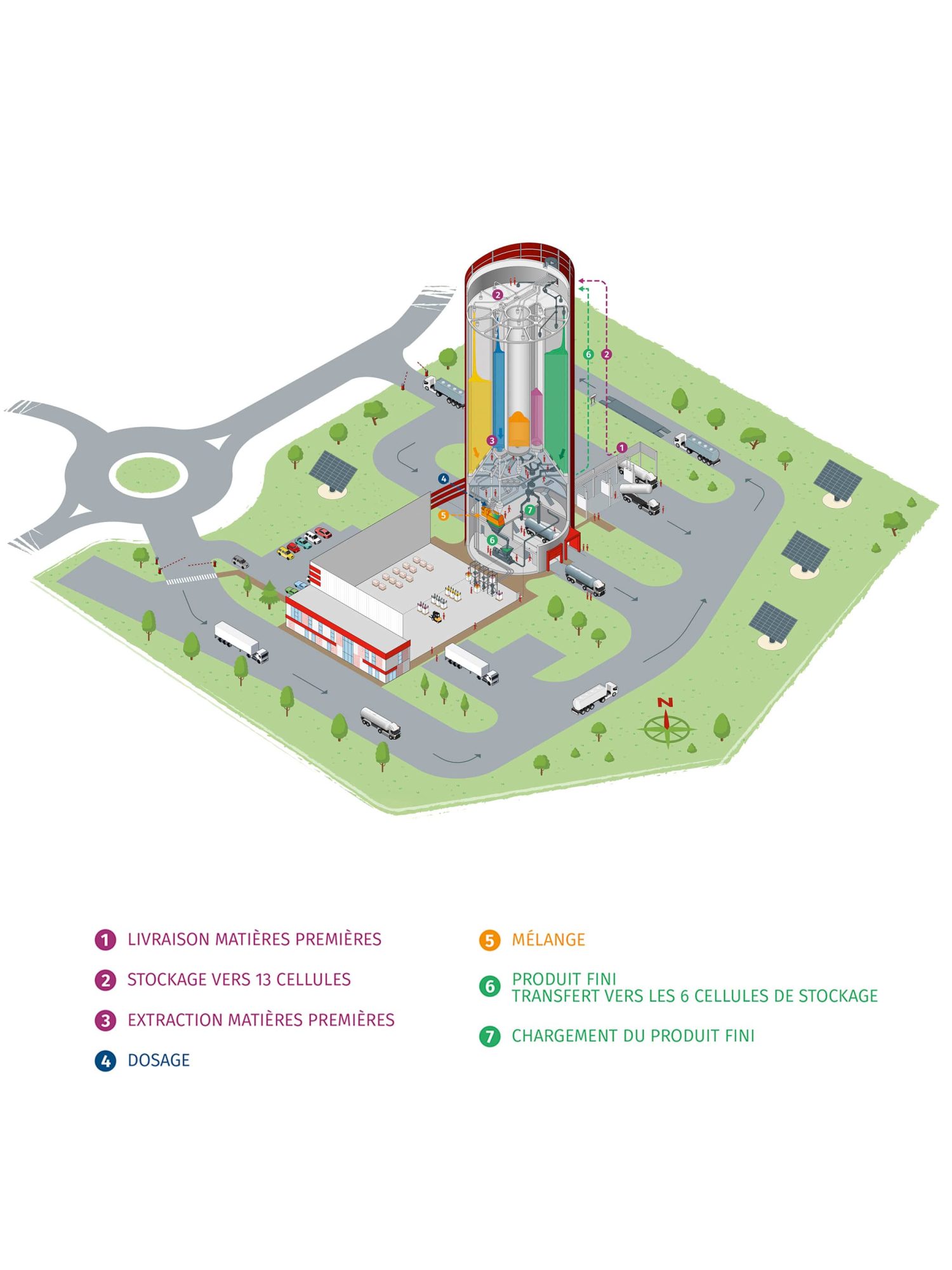
H2, a technological and ecological feat
This new H2 plant is the result of a host of challenges: inventing a large-scale production process, combining industrial performance with minimum impact, and combining industrial production capacity with a small footprint.
By opting for a vertical production model, we have been able to limit the amount of land we take up and meet the Zero Net Artificialisation (ZAN) targets set by the public authorities. This small footprint also makes it easier to locate in future development zones, with limited land requirements.
The vertical model also makes it possible to use gravity to optimise the production process. It is simpler and less energy-consuming to transport powdered materials by gravity than by conveyors or belts: less waste, less dust, less energy…
Hoffmann Green has also designed an intelligent, fully connected production process. The plant can be controlled using a global intelligent programme. A human/machine/digital alliance that optimises every stage and guarantees a high standard of quality.
Finally, the plant is over 50% self-sufficient in energy, thanks to the installation of 12 solar trackers.
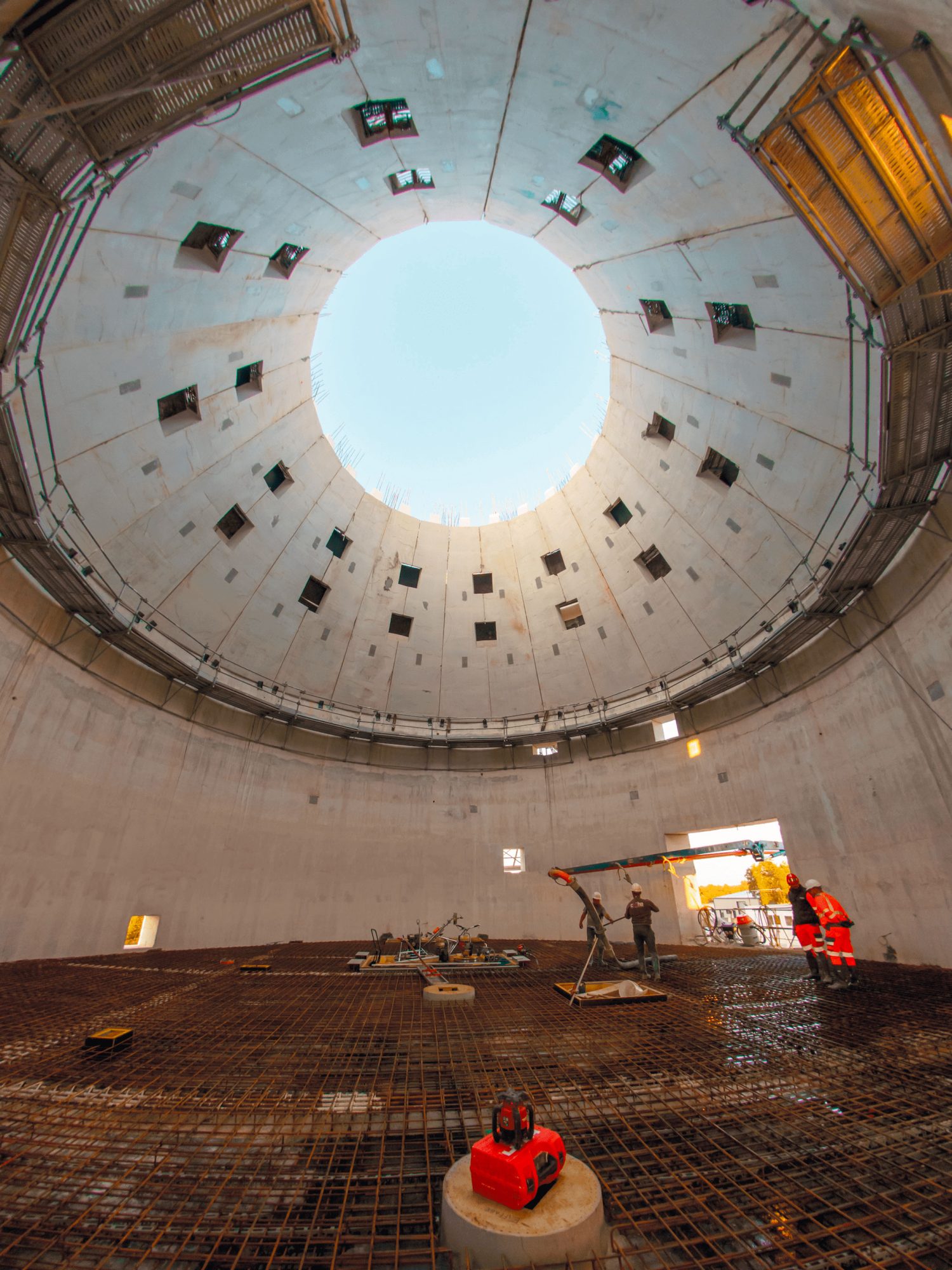
A civil engineering tour de force
H2 is first and foremost a major innovation in terms of its design and production.
Made entirely from Hoffmann Green concrete, it is yet another example of the performance of these new cements.
Designed by Ibau Hamburg and built by Eiffage Génie Civil teams using 1.80 m smooth formwork, H2 is a feat of engineering.
The first part, up to 20 metres, was completed before 24 petals weighing 15 tonnes each were laid, prefabricated on site using concrete made from H-UKR 0% clinker cement, to form the inverted cone of the installation.
This was a fine demonstration of the quality of Hoffmann Green’s technologies, which successfully passed all the CSTB pull-out tests on the lifting elements.
The second part of the lift, from 20 to 70 metres, was carried out continuously over 22 consecutive days, 24 hours a day.
- 22million euro budget
- 1 000tonnes of cement produced per day
- 70metres high
- 100 %made of Hoffmann Green 0% clinker cement
- 24months of work
