“Interview with David Hoffmann, Managing Director and Scientist – Co-founder of Hoffmann Green
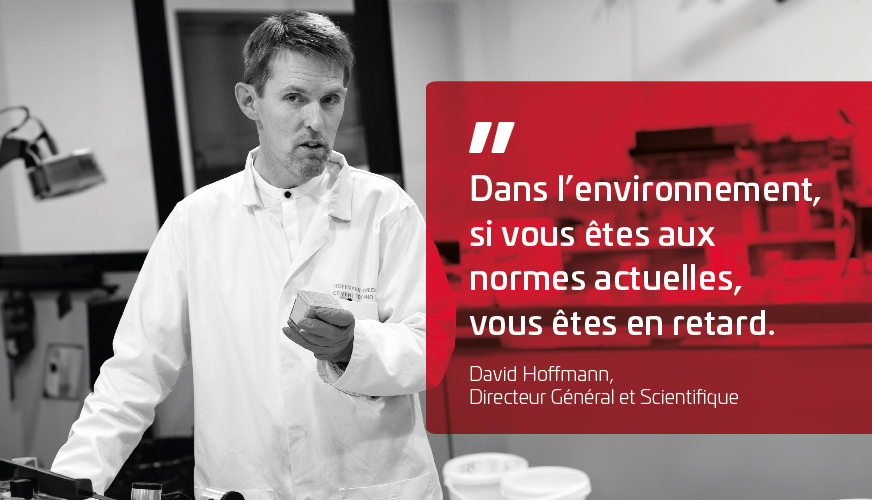
David Hoffmann prefers the calm of the laboratory to the limelight. From his headquarters in the heart of the Vendée region of France, Hoffmann Green is nevertheless the father of breakthrough technologies that are unique in the world. The new cements that bear his name are the first truly carbon-free cements available. But how did the work of a waste chemist become cement produced on an industrial scale? Interview with a man whose words are as rare as his ambition is great.
David Hoffmann, what guides your work?
I want to leave a livable planet to my children. This was my first motivation and the origin of an early awareness. I used to work in toxic waste treatment. My job was to find solutions to render them inert. France is number 1 in this sector. But at the same time, I became aware of the pollution linked to waste all over the world and the consequences for future generations. I’ve always worked to reduce this footprint.
How do you go from processing waste to inventing new cements?
I worked for the Séché Environnement group. My role was to find binder formulas to render toxic waste inert. That’s how I came to explore alternatives to Portland cements. I came up with geoplymers and metakaolins, for example. But I wanted to find broader applications than just the waste sector. So, in parallel with my job, I set up my own business and a laboratory in my garage. It was then, in 2014, that I met Julien Blanchard.
Less than ten years after you met, Hoffmann Green Cement has become the sixth in this meteoric rise?
From the outset, we’ve been focused on the result. We’re very pragmatic. I don’t want to do things that are pointless. I have this culture of research that has to find something. One example: our H-IONA cement was certified in six months using an Afnor standard. We identified a lead and the whole team rallied round to achieve this very tight deadline. I also think we’re efficient because we’ve brought everything in-house. This means, for example, that we can carry out our own tests and controls. Right from the research phase, we integrate the “factory” dimension. The various stages are brought closer together and the different departments work together. This makes us faster and more efficient.
How does Hoffmann Green come up with a breakthrough innovation?
Research always starts from someone else’s work. I read what’s out there and try to add to it by going where others don’t go. I believe that intuition is a form of rationality before explanations are found. So we develop breakthrough solutions which we then adapt to applications and markets. Right from the R&D phase, we integrate production constraints such as price and availability of raw materials. In the laboratory, we test on small formats to be agile. If it doesn’t work, we try again. And at the end of the process, we have a miniature pilot plant that enables us to test on a small scale. As the factory is entirely digital, all we have to do is multiply the quantities to produce on an industrial scale.
How do you imagine each innovation?
What guides me is simplicity. In formulation and application. Then each customer has his or her own constraints, and we try to meet them. It’s a culture that comes to me from the world of waste, where it’s the result that counts. You have to develop solutions that solve problems as cleanly and cheaply as possible. We apply this philosophy at Hoffmann Green. It’s a radically different approach from that of traditional cement manufacturers, who have standard products that it’s up to builders to adapt to. Our job is to respond to the constraints of others.
One constraint you’ve had to face is the standard. The construction industry is highly standardized. How did you go about “standardizing” your new cements?
In the environment, if you’re up to current standards, you’re behind the times. So we’re always looking to go beyond it to create a new one. Construction standards are linked to a method, a procedure, a way of doing things. But above all, it is established according to Portland cement criteria. So we had to go through all the certification stages. Every innovation takes a long time to prove its performance. Even more so in a closed and very conservative market. But our job is not to be standardized, it’s to find solutions.
This interview is taken from pages 2 and 3 of our ForHummagazine , currently available for free consultation on our website.